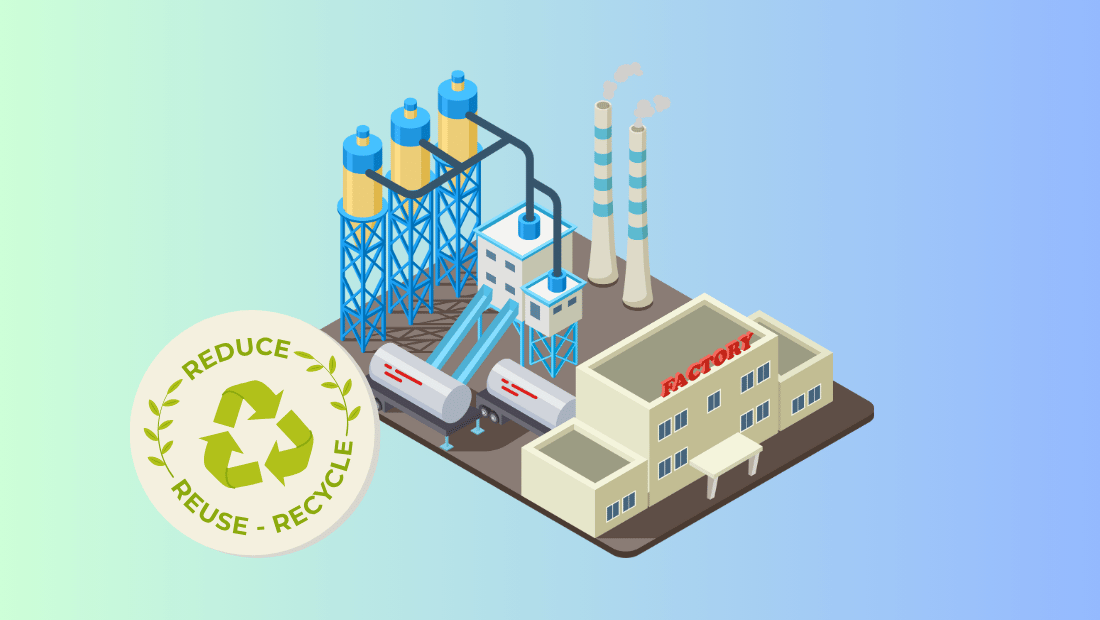
Understanding Lean Manufacturing
What is Lean Manufacturing?
Lean manufacturing is a production methodology that emphasizes the elimination of waste within a manufacturing system. It is founded on the core principles of maximizing value by reducing waste and improving efficiency. Lean manufacturing focuses on streamlining processes, optimizing resource use, and implementing a culture of continuous improvement. These principles are designed to enhance productivity while minimizing costs and environmental impact.
The central tenet of lean manufacturing is to deliver value from the customer's perspective. This means identifying and eliminating activities that do not add value to the end product, known as non-value-added activities. By focusing on the reduction of waste, lean manufacturing helps businesses to not only cut costs but also to enhance the quality and timeliness of their products.
Waste reduction is critical in production processes, as it directly impacts operational efficiency and profitability. By minimizing waste, manufacturers can improve their bottom line while also contributing to sustainability goals. For a deeper dive into lean waste reduction strategies, visit Lean Waste Reduction Strategies.
The Role of Lean Principles in Modern Manufacturing
In modern manufacturing, the application of lean principles is increasingly essential for staying competitive. Lean methodologies are applied through various practices such as Just-In-Time (JIT) production, which reduces inventory costs by receiving goods only as they are needed in the production process, and Kaizen, which promotes a culture of continuous, incremental improvement.
Adopting lean methodologies offers numerous benefits, including enhanced production efficiency, improved product quality, and increased customer satisfaction. By focusing on value creation and waste elimination, organizations can achieve significant improvements in their operational processes. Moreover, lean manufacturing encourages employee involvement, fostering a proactive workplace culture where employees are engaged and empowered to contribute to process improvements.
For more insights into the fundamentals of lean manufacturing strategies, principles, and waste reduction, explore Exploring the Fundamentals of Lean Manufacturing Strategies, Principles, and Waste Reduction.
As manufacturing evolves, the integration of lean principles is becoming more pronounced with the use of advanced technologies and data-driven decision-making. Companies implementing lean manufacturing often utilize tools such as value stream mapping and process mapping to identify and eliminate waste effectively. These tools provide a clear visual representation of the production flow, highlighting areas where waste occurs and opportunities for improvement.
To further explore how lean principles can enhance your production processes, consider using our Lean Manufacturing Checklist Guide to ensure your manufacturing processes are optimized for efficiency and waste reduction.
By adopting lean manufacturing, businesses not only enhance their competitive advantage but also contribute to sustainable practices that are increasingly demanded by consumers and regulatory bodies alike. To stay current on lean manufacturing trends and strategies, check out Top Lean Manufacturing Principles to Reduce Waste.
Identifying and Reducing Waste in Manufacturing
Types of Waste in Manufacturing
In the realm of lean manufacturing, understanding the different types of waste is crucial for improving efficiency. These wastes, often referred to as the "8 Wastes of Lean," include unnecessary movement, overproduction, waiting (idle time), excess inventory, unnecessary processing, defects, underutilization of talent, and transportation. Recognizing these elements as non-value-added activities is the first step toward their elimination.
Unnecessary movement involves any motion that does not add value to the product, such as employees searching for tools or parts. Overproduction refers to manufacturing more than is needed, leading to excess inventory and wasted resources. Idle time represents periods where workers or machines are waiting due to imbalances in the production line. Excess inventory ties up capital and space, while unnecessary processing involves steps that do not enhance the product's value.
Defects require additional resources to address, and underutilization of talent occurs when employees' skills are not fully leveraged. Transportation waste arises from unnecessary movement of products between locations, which can be minimized through strategic layout planning. To dive deeper into eliminating these wastes, explore Tools and Techniques to Eliminate the 8 Wastes of Lean Manufacturing.
Effective Waste Reduction Strategies
Minimizing waste in manufacturing requires strategic approaches. One effective strategy is implementing Just-In-Time (JIT) production, which aims to reduce inventory waste by aligning production schedules with demand. This method helps decrease the costs associated with storing excess inventory and allows for a more agile response to market changes.
Another powerful tool is value stream mapping, which provides a visual representation of the production process, identifying areas where waste can be eliminated. This technique enables manufacturers to focus on streamlining operations and improving the flow of materials and information. For more on how value stream mapping can aid in waste reduction, see How to Reduce Manufacturing Waste.
Real-world examples demonstrate the success of waste reduction initiatives. For instance, Toyota's lean manufacturing system has become a benchmark for effective waste reduction, emphasizing continuous improvement (Kaizen) and employee involvement, which are critical for sustaining long-term efficiency. Companies adopting these strategies report significant reductions in waste and improvements in both productivity and product quality.
At Manifestly, we understand the importance of structured processes in waste reduction. Our Lean Manufacturing Checklist Guide is designed to help manufacturers systematically identify and eliminate waste, ensuring that production processes are optimized for maximum efficiency.
To further explore strategies and tools for effective waste reduction, consider examining our wide range of workflow templates tailored for the manufacturing sector. Visit Manufacturing Workflow Templates for detailed guidance and practical solutions to streamline your operations.
Integrating these waste reduction strategies not only boosts operational efficiency but also aligns with sustainability goals, which are increasingly vital in today's competitive manufacturing landscape. For a comprehensive guide on lean continuous improvement, explore Lean Continuous Improvement.
Implementing Lean Tools for Process Efficiency
Value Stream Mapping and Process Mapping
One of the core strategies in lean manufacturing is the use of value stream mapping (VSM). This tool is instrumental in identifying and eliminating waste in manufacturing processes. Value stream mapping provides a visual representation of the entire production process, highlighting both value-added and non-value-added activities. This visualization allows teams to pinpoint inefficiencies and areas of waste, such as delays and bottlenecks, that can be targeted for improvement.
Process mapping complements VSM by detailing the specific steps involved in a process and identifying redundancies or unnecessary complexities. By laying out each step, manufacturers can streamline operations, ensuring that only essential activities that add value are retained. This meticulous approach to process analysis is crucial for aligning production with lean objectives, ultimately reducing costs and enhancing productivity. For more insights into how these tools aid in waste reduction, visit How to Reduce Manufacturing Waste.
Leveraging Lean Tools for Operational Waste Reduction
Beyond mapping, several lean tools play a pivotal role in operational waste reduction. Just-In-Time (JIT) production is one such tool that aligns manufacturing schedules with demand, minimizing inventory waste. This approach reduces the costs associated with excess inventory storage and enhances flexibility in response to market fluctuations. Adopting JIT can lead to substantial efficiency gains by ensuring resources are utilized only when necessary.
Another significant lean tool is Kanban, which helps manage work processes by using visual cues to signal when more resources are needed. This system helps maintain optimal workflow and prevents overproduction, a common source of waste. Similarly, 5S methodology—Sort, Set in order, Shine, Standardize, Sustain—ensures that the workplace is organized and efficient, reducing time waste and enhancing safety.
Inventory management plays a crucial role in lean manufacturing, as it focuses on balancing inventory levels to meet production needs without excess. Effective inventory management reduces waste by preventing overstocking and understocking, thus optimizing the use of materials and resources. For a deeper understanding of effective inventory management strategies, explore our SOP Software Solutions to Skyrocket Productivity.
Incorporating these lean tools into your manufacturing processes not only reduces operational waste but also contributes to a more agile and competitive production environment. By leveraging advancements in lean manufacturing, businesses can achieve higher efficiency, lower costs, and enhanced product quality. For a comprehensive guide on implementing these strategies, you can explore our Lean Manufacturing Checklist Guide.
At Manifestly, we offer a range of workflow templates specific to Manufacturing to help streamline your operations and integrate lean tools effectively. These templates are designed to assist manufacturers in systematically applying lean principles, ensuring that their processes are not only efficient but also aligned with industry best practices for waste reduction and resource optimization.
By utilizing these lean tools, manufacturers can significantly reduce waste and increase efficiency, aligning with the sustainability goals that are becoming increasingly important in today's market. To stay ahead in the competitive landscape, it is essential to continuously adapt and refine your processes using these proven lean methodologies.
Continuous Improvement and Employee Involvement
The Importance of Continuous Improvement
Continuous improvement is a cornerstone of lean manufacturing, driving companies to constantly refine their processes, reduce waste, and enhance efficiency. Fostering a culture of continuous improvement means encouraging every employee to seek opportunities for enhancement in their daily tasks. This approach not only boosts productivity but also helps organizations remain competitive in the fast-paced manufacturing sector.
One effective method of implementing continuous improvement is through the Kaizen philosophy, which promotes small, incremental changes. By focusing on gradual improvements, manufacturers can significantly enhance their operations over time. For instance, Toyota, a leader in lean manufacturing, uses Kaizen to empower workers at all levels to suggest improvements, resulting in more efficient production lines and higher quality products. For more on the principles of lean continuous improvement, visit Lean Continuous Improvement.
Additionally, continuous improvement can be supported by utilizing detailed process documentation and analysis tools, such as those offered by Manifestly. By using checklists and workflows, manufacturers can systematically identify areas for improvement and track their progress over time. These tools ensure that improvements are not only implemented but also sustained, leading to long-term success. For more on how checklists can enhance operational efficiency, see How Checklists Can Systematize Your Business.
Encouraging Employee Involvement
Employee involvement is crucial for the success of lean manufacturing initiatives. By engaging employees in waste reduction efforts, companies can leverage their unique insights and experiences to identify areas where waste occurs and develop innovative solutions. Encouraging this involvement not only enhances process efficiency but also boosts employee morale and job satisfaction.
One strategy to encourage employee involvement is to establish cross-functional teams that bring together employees from different departments. These teams can collaborate to identify inefficiencies and brainstorm solutions. Additionally, providing employees with training and resources, such as the Continuous Improvement Checklist, empowers them to actively participate in improvement initiatives.
Moreover, recognition and rewards for employee contributions can further motivate team members to engage in continuous improvement. Recognizing the efforts and successes of employees not only reinforces a culture of improvement but also encourages the sharing of best practices across the organization.
Involving employees in the improvement process has numerous benefits, including the identification of previously overlooked opportunities for enhancement. Employees who work directly with processes often have valuable insights into potential improvements, which can lead to significant waste reduction and efficiency gains. For more tips on engaging employees in process improvement, explore our Mastering Operational Efficiency: The Power of Checklists.
By fostering a culture of continuous improvement and actively involving employees, manufacturers can create a dynamic and efficient production environment that adapts to changes and maintains a competitive edge. To explore more strategies for continuous improvement and employee involvement in manufacturing, visit our Manufacturing Workflow Templates for practical solutions and tools to streamline your operations.
Sustainable Manufacturing and Resource Optimization
Achieving Sustainable Manufacturing
In the quest for a greener future, lean manufacturing plays a pivotal role in promoting sustainability. By focusing on waste reduction and efficiency, lean principles inherently align with sustainable practices. Lean manufacturing encourages the use of fewer resources, minimizing waste and energy consumption, which contributes to a reduced environmental footprint. By implementing lean methods, manufacturers can significantly lower their carbon emissions and resource usage, paving the way for a more sustainable production process.
One of the key sustainable practices in manufacturing is the adoption of a circular economy model. This involves designing products with their entire lifecycle in mind, ensuring that materials can be reused or recycled at the end of their life. Companies like Interface, a global leader in commercial flooring, have successfully integrated circular economy principles by using recycled materials in their products and ensuring their carpets can be easily recycled, thus reducing waste.
Another example is the widespread implementation of energy-efficient technologies. Manufacturers are increasingly investing in machinery and equipment that consume less energy, thereby decreasing their overall energy consumption. This not only reduces costs but also aligns with global sustainability goals. Additionally, initiatives such as zero-waste manufacturing aim to completely eliminate waste by recycling and reusing materials within the production process. For manufacturers seeking to integrate sustainability into their operations, exploring a Sustainability Practices Checklist can provide valuable insights and actionable steps.
Optimizing Resources for Cost Savings
Resource optimization is a cornerstone of lean manufacturing, offering significant opportunities for cost savings. By maximizing the efficiency of resource use, manufacturers can reduce costs while maintaining high-quality production standards. Techniques such as Just-In-Time (JIT) inventory management help in minimizing storage costs and reducing waste caused by overproduction. By aligning production schedules closely with demand, manufacturers can ensure that resources are only used when necessary, leading to substantial cost reductions.
Another effective resource optimization technique is the implementation of predictive maintenance. By using advanced data analytics and IoT technologies, manufacturers can predict equipment failures before they occur, allowing for timely maintenance. This approach not only extends the lifespan of machinery but also prevents costly downtime and repairs. Embracing tools like a Preventive Maintenance Checklist can guide manufacturers in establishing a robust maintenance schedule that optimizes resource use and reduces costs.
Furthermore, leveraging data-driven decision-making through sophisticated analytics can enhance resource allocation and streamline operations. By understanding production patterns and resource consumption, manufacturers can make informed decisions that optimize resource use and enhance overall efficiency. For organizations looking to refine their processes, exploring Lean Continuous Improvement strategies can provide comprehensive guidance on achieving both resource optimization and cost savings.
Ultimately, optimizing resources not only leads to immediate cost savings but also supports long-term sustainability goals. By ensuring efficient use of materials and energy, manufacturers can contribute to a more sustainable future while simultaneously enhancing their bottom line. To further explore how lean manufacturing can aid in resource optimization and sustainability, visit our Manufacturing Workflow Templates for industry-specific solutions.
FAQ on Lean Manufacturing and Waste Reduction
Common Questions about Lean Manufacturing
What are the key benefits of lean manufacturing?
Lean manufacturing offers several significant benefits, primarily focusing on waste reduction and efficiency enhancement. By eliminating non-value-added activities, lean practices help in streamlining operations, thereby reducing costs and improving product quality. This approach not only enhances customer satisfaction by delivering high-quality products on time but also supports sustainability goals by minimizing resource usage and waste. For more insights into the benefits and principles of lean manufacturing, explore Exploring the Fundamentals of Lean Manufacturing Strategies, Principles, and Waste Reduction.
How can lean tools help in waste reduction?
Lean tools such as Just-In-Time (JIT) production, value stream mapping, and 5S methodology are instrumental in identifying and eliminating waste in manufacturing processes. JIT reduces inventory waste by synchronizing production schedules with demand. Value stream mapping provides a detailed visual of production processes, pinpointing inefficiencies and areas where waste occurs. The 5S methodology organizes the workplace to enhance efficiency and safety. To understand how these tools can be applied to your operations, visit Lean Waste Reduction Strategies.
Addressing Concerns about Implementation
How to overcome challenges in implementing lean strategies?
Implementing lean strategies can present challenges such as resistance to change and the need for cultural shifts within an organization. Overcoming these challenges requires a commitment to continuous improvement and employee engagement. Providing training and resources, such as a Continuous Improvement Checklist, can empower employees to embrace lean methodologies. Additionally, leadership involvement is crucial in guiding the organization through the transition and ensuring alignment with lean objectives.
Tips for ensuring successful lean transformation
Successful lean transformation hinges on fostering a culture of continuous improvement and involving employees at all levels. Encouraging open communication and collaboration across departments can facilitate the identification of waste and the development of innovative solutions. Utilizing workflow templates, such as those available in our Manufacturing Workflow Templates, can provide a structured approach to implementing lean practices and tracking progress. Additionally, setting clear goals and regularly reviewing achievements can help sustain momentum and drive continuous improvement.
For additional resources on overcoming challenges and ensuring a smooth lean transformation, consider exploring our blog post on Mastering Operational Efficiency: The Power of Checklists, which offers practical tips and strategies for integrating lean principles into your manufacturing processes.
Why Choose Manifestly for Your Lean Manufacturing Needs
Personalized Demos and Support
At Manifestly, we understand that lean manufacturing is not just about implementing generic strategies but tailoring solutions that fit the unique needs of your business. Our personalized demos are designed to help you grasp the nuances of lean tools, ensuring you can effectively integrate them into your operations. These demos provide a hands-on experience, allowing you to see firsthand how our solutions can optimize your processes and eliminate waste.
Beyond our demos, we offer access to a comprehensive help center, where you can find resources and support for ongoing queries and challenges. Whether you're looking to refine your lean strategies or need assistance with specific tools, our customer support team is always ready to guide you. Learn more about how our personalized demos can transform your lean manufacturing journey.
Tailored Solutions for Your Business
Every manufacturing process is unique, which is why we offer customized checklists to suit your specific needs. Our solutions are designed to align perfectly with your operational processes, allowing you to focus on what matters most: efficiency and waste reduction. By utilizing our tailored checklists, you can streamline your workflow, improve productivity, and significantly reduce waste.
Manifestly's SOP software solutions are particularly beneficial for manufacturing businesses looking to enhance their operational efficiency. These solutions help in establishing clear procedures and protocols, ensuring consistency and quality across all production lines. Moreover, our Lean Manufacturing Checklist Guide provides a step-by-step approach to implementing lean principles, helping you stay ahead in the competitive manufacturing landscape.
By choosing Manifestly, you're not only opting for a provider with a track record of excellence but also a partner committed to your success. Our solutions are recognized as top business process management software, ensuring you receive the best tools and support for your lean manufacturing needs. To explore more about how Manifestly can enhance your manufacturing processes, visit our Manufacturing Workflow Templates for industry-specific solutions.
Related Blog Posts
Explore More on Lean Manufacturing
To delve deeper into lean manufacturing practices, consider reading about the Top Lean Manufacturing Principles to Reduce Waste. This resource provides insights into fundamental principles that can help reduce waste and improve efficiency within manufacturing processes.
For a comprehensive understanding of how to tackle the eight types of waste in lean manufacturing, explore Tools and Techniques to Eliminate the 8 Wastes of Lean Manufacturing. This article offers valuable strategies for identifying and eliminating waste, leading to more streamlined operations.
Further Reading on Waste Reduction Strategies
To learn more about continuous improvement in lean manufacturing, check out Lean Continuous Improvement. This blog post discusses how continuous improvement is vital for maintaining efficiency and effectiveness in manufacturing processes.
For insights into effective inventory management as a part of waste reduction strategies, visit How to Reduce Manufacturing Waste. This resource highlights techniques for inventory management that minimize waste and optimize resource usage.
For more practical solutions and tools to implement these strategies, explore our Manufacturing Workflow Templates which provide detailed guidance on streamlining operations.