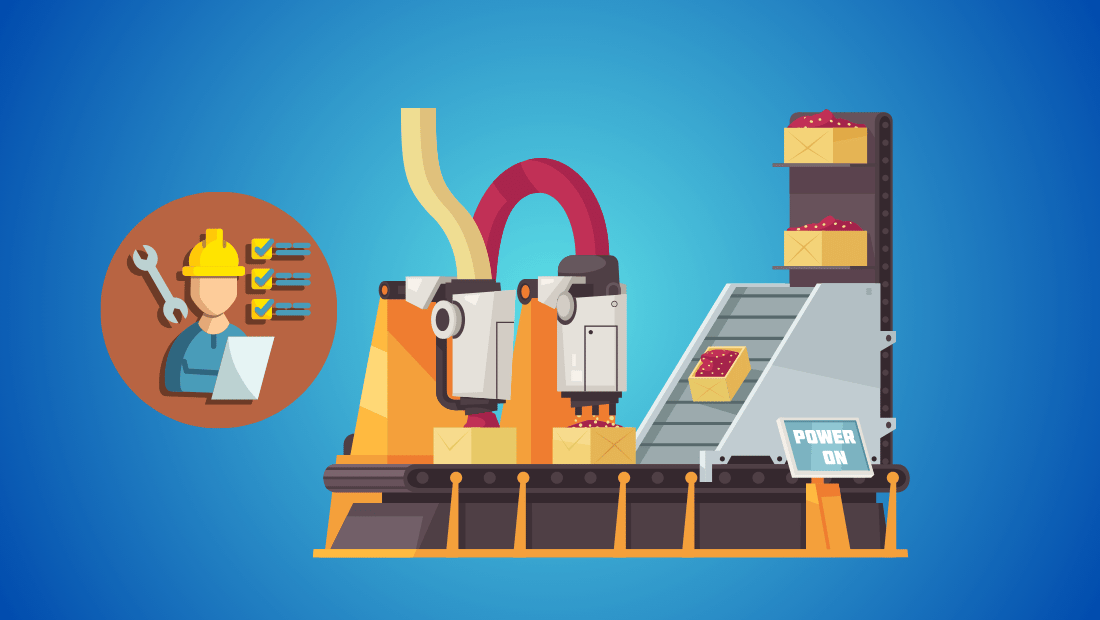
Understanding Predictive Maintenance in Manufacturing
What is Predictive Maintenance?
Predictive maintenance is a proactive approach to managing industrial machinery by using data-driven insights to predict when equipment might fail or require servicing. Unlike reactive maintenance, which responds to equipment failures after they occur, or preventative maintenance, which follows a predetermined schedule, predictive maintenance leverages advanced technologies such as sensors, machine learning, and data analytics to assess the actual condition of equipment.
The core principle of predictive maintenance revolves around the continuous monitoring of machinery through various data inputs, such as temperature, vibration, and performance metrics. By analyzing this data, manufacturers can make informed decisions about when to perform maintenance, thereby reducing the likelihood of unexpected breakdowns and minimizing operational disruptions. For a deeper dive into predictive maintenance, you can explore more about Predictive Maintenance in Manufacturing.
Benefits of Predictive Maintenance for Industrial Machinery
Implementing predictive maintenance in manufacturing can lead to significant improvements in operational efficiency and cost savings. Here are some key benefits:
- Reducing Downtime: Predictive maintenance drastically reduces unplanned downtime by identifying potential issues before they lead to equipment failures. This proactive approach ensures that machinery is serviced at the optimal time, preventing costly interruptions in production. Learn more about how predictive maintenance can impact manufacturing by visiting The Impact of Predictive Maintenance on Manufacturing.
- Extending Equipment Lifespan: Regular monitoring and timely maintenance can significantly extend the lifespan of industrial machinery. By preventing excessive wear and tear, manufacturers can maximize the return on investment for their equipment purchases.
- Lowering Labor and Repair Costs: Predictive maintenance allows for more efficient use of maintenance resources. By scheduling maintenance only when necessary, companies can allocate their labor more effectively and reduce repair costs associated with emergency fixes. This approach not only saves money but also frees up maintenance staff to focus on other critical tasks.
For manufacturers looking to enhance their workflow management, integrating predictive maintenance solutions can be a game-changer. By utilizing checklists and advanced data analytics, companies can streamline their maintenance processes and improve overall efficiency. To explore more about optimizing manufacturing operations, check out 10+1 Best Workflow Management Software 2024 For Maximum Efficiency.
As Industry 4.0 continues to evolve, predictive maintenance remains a cornerstone of smart factory initiatives. By embracing these technologies, manufacturers can not only safeguard their equipment but also gain a competitive edge in the rapidly changing industrial landscape. For further insights into Industry 4.0 and predictive maintenance, you might find A Guide to Industry 4.0 Predictive Maintenance enlightening.
Predictive Maintenance Solutions for Manufacturing Equipment
AI-Powered Predictive Maintenance Tools for Factories
The integration of artificial intelligence (AI) within predictive maintenance solutions is transforming the manufacturing industry. AI algorithms are capable of analyzing vast amounts of data to create predictive models that forecast equipment failures before they occur. By utilizing machine learning, these models continuously improve as they receive data, allowing manufacturers to anticipate maintenance needs with increasing accuracy. This proactive approach significantly reduces downtime and optimizes maintenance schedules, ensuring that factories operate at peak efficiency.
Real-time monitoring of industrial machinery is another significant advantage of AI-powered predictive maintenance tools. These systems provide continuous oversight of equipment conditions, enabling immediate responses to potential issues. This not only prevents catastrophic failures but also extends the lifespan of equipment by addressing minor issues before they become major problems. For a deeper understanding of how AI can enhance predictive maintenance, refer to Predictive Maintenance and the Smart Factory.
Sensor-Based Predictive Maintenance for Machines
Sensors play a crucial role in predictive maintenance by providing real-time data on equipment conditions. Temperature and vibration sensors are particularly valuable for condition-based monitoring, offering insights into the operational state of machinery. These sensors detect anomalies that may indicate a potential failure, allowing maintenance teams to address issues before they lead to equipment downtime.
The deployment of sensor-based systems enables timely repairs and reduces the reliance on scheduled maintenance, which can be both time-consuming and costly. By capturing real-time data, manufacturers can shift to a more dynamic maintenance strategy that aligns with the actual condition of the equipment. For more information on sensor-based predictive maintenance, consider exploring Predictive Maintenance in Manufacturing.
Leveraging IoT for Predictive Maintenance in Manufacturing
The Internet of Things (IoT) has become an integral part of predictive maintenance strategies in manufacturing. IoT devices provide real-time diagnostics and insights into the health of machinery, facilitating a more connected and responsive maintenance system. By integrating IoT sensors and devices, manufacturers can monitor equipment performance continuously, ensuring that any anomalies are detected and addressed promptly.
The impact of IoT on the production environment and factory floor is profound. It enhances operational efficiency by reducing unplanned downtime and optimizing resource allocation. IoT-based predictive maintenance systems also contribute to better decision-making by providing detailed analytics on equipment performance. This leads to more informed maintenance strategies and improved production outcomes. Explore further insights on IoT integration in manufacturing predictive maintenance by visiting A Guide to Industry 4.0 Predictive Maintenance.
Adopting these predictive maintenance solutions not only improves equipment longevity but also streamlines manufacturing operations. For manufacturers seeking to enhance their maintenance strategies, leveraging advanced technologies and data analytics is key. To explore more on how checklist systems can support your predictive maintenance efforts, check out How Checklists Can Systematize Your Business and explore relevant workflow templates specific to Manufacturing.
Implementing Predictive Analytics in Manufacturing Maintenance
Predictive Analytics in Manufacturing Maintenance
Predictive analytics plays a pivotal role in enhancing manufacturing maintenance processes. By leveraging advanced analytical methods, manufacturers can transform raw data into actionable insights, allowing for precise prediction of machine failures. These analytics utilize historical data and real-time input from connected devices to identify patterns and trends that may indicate potential malfunctions. The ability to predict equipment issues before they occur enables maintenance managers to schedule interventions at optimal times, thereby avoiding costly disruptions. For a deeper understanding of how predictive analytics is reshaping manufacturing, delve into How Predictive Maintenance is Improving Manufacturing.
Data-driven insights empower maintenance managers by providing a comprehensive overview of machinery health. This approach facilitates informed decision-making, allowing managers to prioritize maintenance tasks based on urgency and impact on production. Additionally, predictive analytics supports the development of more efficient maintenance schedules, improving resource allocation and reducing unnecessary checks. The impact of data analytics in manufacturing maintenance is profound, as it not only enhances operational efficiency but also extends the lifespan of critical equipment. For further exploration of predictive analytics in manufacturing, you can access resources like Predictive Maintenance in Manufacturing.
Predictive Maintenance Software for Industrial Equipment
Predictive maintenance software is an essential component in the modern manufacturing landscape. These software solutions are designed to collect, analyze, and interpret vast amounts of data from various sources, including IoT sensors and historical maintenance records. One of the notable features of predictive maintenance software is its ability to provide real-time condition monitoring and diagnostics, which significantly enhances the ability to foresee equipment failures. This proactive approach ensures that maintenance activities are conducted based on the actual state of the machinery rather than on predetermined schedules, which can be inefficient and costly.
The software also aids in minimizing unplanned downtime by automating the detection of anomalies and potential issues. This automation allows for swift interventions, reducing the risk of unexpected breakdowns that can halt production lines and result in substantial financial losses. Moreover, predictive maintenance software often includes features for generating maintenance reports and analytics dashboards, which provide valuable insights into equipment performance and maintenance trends. By adopting these software solutions, manufacturers can achieve a more streamlined and efficient maintenance process. To learn more about the features and benefits of predictive maintenance software, consider visiting The Impact of Predictive Maintenance on Manufacturing.
For companies aiming to integrate predictive maintenance into their operations, utilizing comprehensive checklists can greatly enhance the implementation process. Manifestly offers a range of workflow templates specific to Manufacturing that can be customized to fit specific operational needs. These templates can help ensure that critical steps are not overlooked, promoting consistency and efficiency in maintenance practices. By using tools like predictive maintenance software and leveraging structured checklists, manufacturers can significantly boost their operational resilience and maintain a competitive edge in the industry.
Developing Predictive Maintenance Strategies for Factories
Best Practices for Predictive Maintenance in Manufacturing
Developing an effective predictive maintenance strategy is crucial for maximizing the operational efficiency and longevity of manufacturing equipment. One of the first steps in establishing a successful predictive maintenance program is to clearly define the objectives and scope of the initiative. This involves identifying the critical machinery that could benefit most from predictive insights and determining the specific data metrics that will be monitored, such as vibration, temperature, and pressure.
Incorporating condition-based maintenance is another best practice that enhances the effectiveness of predictive strategies. Condition-based maintenance relies on real-time data to determine the health and performance of equipment, allowing maintenance activities to be scheduled based on the actual condition of the machinery rather than a predetermined timeline. This approach not only reduces unnecessary maintenance but also prevents unexpected equipment failures, leading to increased uptime and cost savings. For more insights on implementing condition-based maintenance, you can explore how Predictive Maintenance in Manufacturing can be incorporated into your factory's maintenance strategy.
Additionally, using advanced analytics and machine learning algorithms to analyze historical and real-time data can significantly improve the accuracy of maintenance predictions. This proactive approach ensures that potential issues are detected early, allowing for timely interventions and reducing the likelihood of costly downtimes. To learn more about integrating predictive analytics into your maintenance strategy, consider exploring Predictive Maintenance in Manufacturing.
Preventative vs. Predictive Maintenance in Manufacturing
Understanding the differences between preventative and predictive maintenance is essential for developing a comprehensive maintenance strategy. Preventative maintenance is based on scheduled intervals and involves regular inspections and servicing of equipment regardless of its condition. While this approach can help prevent some failures, it often leads to over-maintenance and unnecessary downtime.
In contrast, predictive maintenance utilizes data-driven insights to predict when maintenance should be performed. By focusing on the actual condition of the equipment, predictive maintenance minimizes the risk of unexpected breakdowns and reduces the frequency of routine maintenance tasks. This leads to more efficient use of resources and a longer lifespan for machinery. The advantages of predictive maintenance over preventative maintenance include reduced maintenance costs, improved reliability, and enhanced operational efficiency. For a more detailed comparison of these maintenance strategies, consider reading How Predictive Maintenance is Improving Manufacturing.
To successfully transition from preventative to predictive maintenance, factories need to invest in the right technology and skills. This involves training maintenance teams to interpret data correctly and make informed decisions based on predictive insights. Additionally, adopting digital tools and software that facilitate real-time monitoring and analytics is crucial for implementing an efficient predictive maintenance program. For those looking to integrate such technologies, relevant workflow templates specific to Manufacturing can be a valuable resource in streamlining the transition process.
By embracing predictive maintenance, manufacturers can revolutionize their maintenance approaches, leading to improved equipment performance and significant cost savings. As factories continue to evolve and adopt Industry 4.0 technologies, predictive maintenance will play an increasingly important role in ensuring operational excellence and competitiveness.
How Predictive Maintenance Improves Manufacturing Efficiency
Reducing Frequency of Repairs and Costly Downtime
Predictive maintenance is a powerful tool for manufacturers aiming to reduce the frequency of repairs and the associated costly downtime. By leveraging advanced technologies such as IoT and AI, companies can anticipate and address potential issues before they lead to equipment failures. This proactive approach allows for more effective scheduling of maintenance activities, focusing on the actual condition of the machinery rather than time-based intervals. As a result, manufacturers can significantly reduce unexpected breakdowns, which are often the leading cause of operational inefficiencies and financial losses.
Implementing predictive maintenance not only helps in minimizing repairs but also enhances the overall operation and efficiency of machines. By maintaining equipment in optimal condition, manufacturers can avoid the productivity loss associated with machine downtime and ensure smoother production workflows. This is particularly important in a competitive manufacturing environment where even a small disruption can have a ripple effect on the supply chain. For further insights into how predictive maintenance can enhance manufacturing efficiency, explore the comprehensive guide on How Predictive Maintenance is Improving Manufacturing.
Case Studies: Successful Implementation of Predictive Maintenance
The successful implementation of predictive maintenance strategies has been documented in various manufacturing settings, showcasing significant improvements in efficiency and operational uptime. For instance, companies that have adopted predictive maintenance have reported a noticeable reduction in downtime, which directly translates to increased production capacity and reduced labor costs. These case studies highlight not only the financial benefits but also the operational advantages of adopting a predictive approach to equipment maintenance.
One such example involves a large-scale manufacturing facility that integrated AI-powered predictive maintenance tools. By doing so, the company was able to predict potential machinery failures with high accuracy, allowing for timely interventions. This not only reduced the frequency of unexpected repairs but also improved the overall reliability of the production line. As a lesson learned from these implementations, it is crucial for manufacturers to invest in the necessary technologies and training to fully leverage predictive maintenance capabilities, thereby maximizing their return on investment. For more detailed examples and insights, visit The Impact of Predictive Maintenance on Manufacturing.
Moreover, the adoption of predictive maintenance strategies aligns with a broader trend towards greater automation and digitalization in manufacturing processes. As the industry continues to evolve towards Industry 4.0, predictive maintenance is becoming increasingly integral to achieving operational excellence. By reducing the reliance on reactive maintenance and enhancing machine efficiency, manufacturers can position themselves more competitively in the market. To explore more on how predictive maintenance can improve manufacturing and to access relevant workflow templates specific to this sector, visit Manufacturing Workflow Templates.
In conclusion, predictive maintenance offers a strategic advantage for manufacturers seeking to improve their operational efficiency and reduce costs. By implementing data-driven maintenance strategies, companies can not only safeguard their equipment but also enhance their overall production capabilities. As more manufacturers realize the potential of predictive maintenance, it is likely to become a standard practice in the pursuit of efficiency and sustainability in manufacturing operations.
Frequently Asked Questions
What are the primary benefits of predictive maintenance?
Predictive maintenance offers several compelling benefits that can transform manufacturing operations. First and foremost, it significantly reduces unexpected breakdowns. By utilizing advanced analytics and real-time data, manufacturers can foresee potential equipment failures before they occur, allowing for timely interventions and minimizing costly production halts. This proactive maintenance approach not only enhances operational efficiency but also contributes to substantial cost savings.
Another major advantage is the increased lifespan of critical machines. Regular monitoring and maintenance based on the actual condition of the equipment prevent excessive wear and tear. This ensures that machinery operates at optimal performance for a longer period, thus maximizing the return on investment. For more in-depth information on the benefits of predictive maintenance, you might consider exploring The Impact of Predictive Maintenance on Manufacturing.
How does predictive maintenance differ from traditional methods?
Predictive maintenance stands apart from traditional maintenance methods primarily through its reliance on data-driven insights rather than routine checks. While traditional methods like preventative maintenance are scheduled based on predetermined intervals, predictive maintenance leverages real-time data to assess the health of equipment continuously. This enables maintenance to be performed only when necessary, thus optimizing resource allocation and reducing unnecessary labor costs.
Another key differentiator is the real-time monitoring capabilities that predictive maintenance offers. By integrating technologies such as IoT sensors and AI, manufacturers can gain immediate insights into equipment performance. This facilitates a more responsive maintenance strategy that can adapt to the actual conditions of the machinery. Such a data-centric approach not only enhances the efficiency of maintenance operations but also allows for more precise decision-making. For a detailed comparison of predictive versus traditional maintenance methods, you can refer to resources like Predictive Maintenance and the Smart Factory.
For those interested in implementing predictive maintenance strategies, using structured checklists can be invaluable. Manifestly offers a range of workflow templates specific to Manufacturing that can help streamline the transition and ensure a consistent approach to maintenance tasks. These tools can greatly enhance your ability to manage maintenance processes efficiently and effectively.
As predictive maintenance continues to evolve with Industry 4.0 technologies, it is poised to become an integral part of modern manufacturing operations. By embracing these advanced maintenance strategies, manufacturers can not only safeguard their equipment but also bolster their competitiveness in the market. For more insights on predictive maintenance and its implementation, consider exploring How Predictive Maintenance is Improving Manufacturing.
Why Choose Manifestly for Predictive Maintenance Solutions?
Personalized Demos and Comprehensive Support
At Manifestly, we understand that every manufacturing environment is unique, which is why we offer personalized demos tailored to your specific needs. These demos provide a hands-on experience of how our checklist solutions can be optimized for your operations. Our team is committed to ensuring that you fully grasp the capabilities of our platform, making the transition to predictive maintenance as smooth as possible. For continuous support, our extensive help center is available to address any queries or challenges you might face, ensuring that your operations run seamlessly.
Tailored Solutions for Your Manufacturing Needs
One of the standout features of Manifestly is our ability to provide customizable checklists specifically designed for factory floor operations. These checklists are not only easy to implement but also flexible enough to adapt to the ever-changing demands of the manufacturing industry. By integrating with existing systems, Manifestly ensures a seamless transition to predictive maintenance, allowing you to focus on enhancing efficiency and reducing downtime.
Our platform also supports workflow process documentation, making it easier to monitor and refine maintenance strategies as your business evolves. This integration capability means that you can leverage existing data and systems without the need for extensive overhauls, ensuring a cost-effective and efficient maintenance solution.
Choosing Manifestly means choosing a partner committed to enhancing your manufacturing processes through innovative and reliable solutions. By focusing on customized support and seamless integration, we provide the tools necessary to optimize your predictive maintenance strategies, ultimately leading to improved operational efficiency and reduced maintenance costs.
Related Blog Posts
Explore More on Predictive Maintenance
As you delve deeper into the world of predictive maintenance, consider expanding your knowledge by exploring a variety of related resources. These articles and guides offer further insights into the strategies, technologies, and innovations shaping the future of manufacturing maintenance.
For a comprehensive understanding of how predictive maintenance is revolutionizing manufacturing, you might find Predictive Maintenance in Manufacturing valuable. It provides a detailed overview of predictive maintenance techniques and their application in reducing downtime and extending equipment lifespan.
To gain insights into the integration of AI and IoT technologies in manufacturing, visit A Guide to Industry 4.0 Predictive Maintenance. This resource explores how these cutting-edge technologies enable real-time data collection and analysis, enhancing decision-making processes and operational efficiency.
For an academic perspective on the impact of predictive maintenance, the paper Predictive Maintenance in the Era of Industry 4.0 offers a deep dive into the methodologies and benefits of adopting predictive strategies in industrial settings.
If you're interested in the role of predictive maintenance in smart factories, check out Deloitte's insights on Predictive Maintenance and the Smart Factory. This article analyzes how smart factory initiatives leverage predictive maintenance to enhance productivity and reduce operational costs.
For more practical advice on implementing predictive maintenance strategies, consider reading The Impact of Predictive Maintenance on Manufacturing. This piece highlights real-world applications and case studies that demonstrate the effectiveness of predictive maintenance in various manufacturing environments.
Lastly, explore our own blog post at Manifestly, 10+1 Best Workflow Management Software 2024 For Maximum Efficiency, to discover tools that can enhance your workflow management and support your predictive maintenance initiatives.
To further streamline your predictive maintenance practices, explore relevant workflow templates specific to Manufacturing available on Manifestly. These resources can assist you in implementing structured and efficient maintenance processes tailored to your operational needs.